Benefits of Electronically Commutated Motors in Industrial Settings
Unless you’re working in a commercial environment, the idea of industrial motor innovation might slip under your radar. But any facility manager can tell you it’s a world of options and decisions.
From AC to DC motors and all sorts of subtypes, industrial motors play a crucial role in transforming energy into motion. Running a big building is expensive and uses a lot of power, so, like with other modern technologies, industrial motor innovation trends toward better energy efficiency and improved performance.
Because of their operating efficiency and other advantages, electrically commutated motors (ECMs) are a popular choice for industrial settings. Let’s explore the why behind their popularity and the key benefits of utilizing this type of motor over others.
Whether relays, transformers, circuit breakers, or more, Functional Devices delivers high-quality electrical components necessary for ECM utilization. If you want to implement ECMs into your power controls and automation, speak with one of our engineers to ensure a holistic approach to your building’s infrastructure.
What Are Electronically Commutated Motors?
Before we explore their benefits, let’s pull back the curtain and look at the basic working principle of an ECM, also known as a three-phase, brushless DC motor.
Here’s how they work step by step:
- The ECM receives power from a power supply, usually an AC voltage.
- A rectifier circuit converts the AC voltage to a DC voltage, which powers the electronic microcontroller.
- The rectified DC feeds into an inverter circuit within the microcontroller.
- The inverter uses high-speed switching transistors to generate a three-phase AC signal controlled in timing and frequency.
- Following a specific sequence, the inverter switches current to the stator windings (conductive coils wound within the stator), creating a rotating magnetic field.
- The rotor, which contains permanent magnets, follows the rotating field and smoothly rotates to complete the motor's working mechanism.
Older motors rely on the mechanical commutation of brushes and a commutator, while ECMs depend on the electronic commutation of an integrated, smart microcontroller. This seemingly small difference, though, has a host of benefits.
Key Benefits of ECMs in Industrial Power Controls
With their incorporated electronics, ECMs are the natural choice for many reasons. Let’s explore their advantages.
Operating Efficiency
One of the most significant selling points of ECMs is their energy efficiency compared to other motors. But how do they accomplish this? They use variable speeds and adjust output in response to load demands.
Think about running the air conditioning in your car. Do you turn it on full blast and then off when you get cold? No, you probably turn down the fan speed and tweak the temperature in response to your comfort level.
ECMs do the same. This responsiveness reduces energy consumption and costs while maintaining desired performance. In fact, the National Institute of Health estimates ECMs could decrease energy usage up to 75 percent!
Precise Control
The same responsiveness that allows for energy efficiency also enables precise control in response to environmental demands. ECMs are a smart choice, especially in applications where consistent performance is essential, like ventilation and pumping systems.
Additionally, ECMs are easily connected to building automation systems (BAS) and can be programmed for precise airflow, speed, and torque ranges. Closed-loop feedback mechanisms ensure that an ECM makes the proper adjustments to maintain performance.
Quiet Operation
Because of their electronic and brushless design, ECMs operate at reduced noise levels compared to motors that contain mechanical parts. That makes them a good option for places where quieter operation is important, such as office spaces, data centers, and medical centers.
Reduced Maintenance
Brushes in mechanical motors need regular maintenance and replacement, but eliminating brushes in ECMs translates to longer lifespans and fewer breakdowns. ECMs experience less physical wear and tear because of their variable speed control and lower operating temperatures, resulting in shorter maintenance downtimes and reduced repair costs.
Give ECMs the Best Infrastructure With Functional Devices
With better energy efficiency, precise and variable control, quiet operation, and reduced maintenance, ECMs make sense for many industrial settings. Consider upgrading your motors for enhanced performance and cost savings. The benefits are too good to pass up!
If you decide to upgrade, don’t forget to look at all the supporting peripheral devices, like relays and power supplies, that will build the infrastructure around your ECMs. That’s where a partner like Functional Devices can help. We’ve been improving operating efficiency in industrial settings for many years. Our building automation relays, power supplies, and other products can help your new ECMs shine. Contact us to discuss a holistic approach for your facility.
About Functional Devices, Inc.
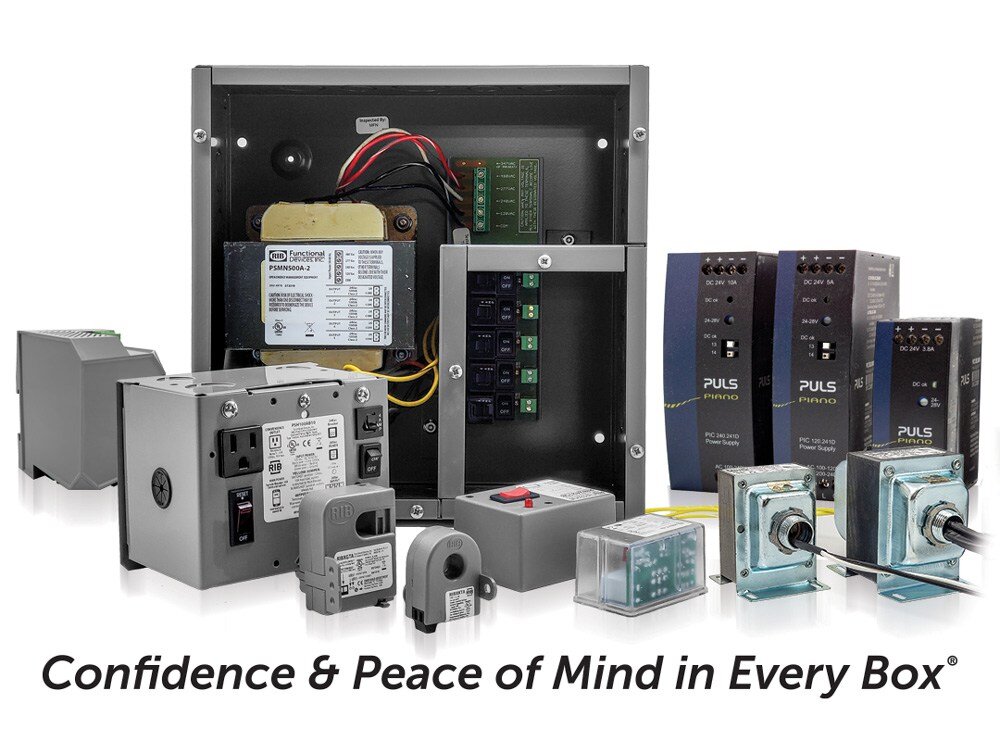
Leaders in the Industry
The world was a very different place in 1969, when Functional Devices, Inc. was founded by engineer and electronics enthusiast Albert Rittmann, but our commitment to evolution and versatility has allowed us to remain a key player in the building automation and lighting controls industry for over 55 years.
Today, as we embrace emerging technology and lean into the future of building automation, our products are still manufactured in the USA with global materials, and we are still committed to our mission of enhancing lives in buildings and beyond. Back in 1969, Albert could never have predicted the technological advances we live with today, but with the groundwork he laid and the vision of his successors, Functional Devices has adapted and grown into a company that can handle anything.